Aluminum Pot Strainer
I don't see them that often but I like the kind of strainer that you hold up to the pot while you just pour the water out. My father made a batch one Christmas and we like using the one he gave us but I love metal and I thought I would try making some out of aluminum.
The overall style of what my dad made seemed good to me so I drew a similar design up in solidworks during a lunch break.
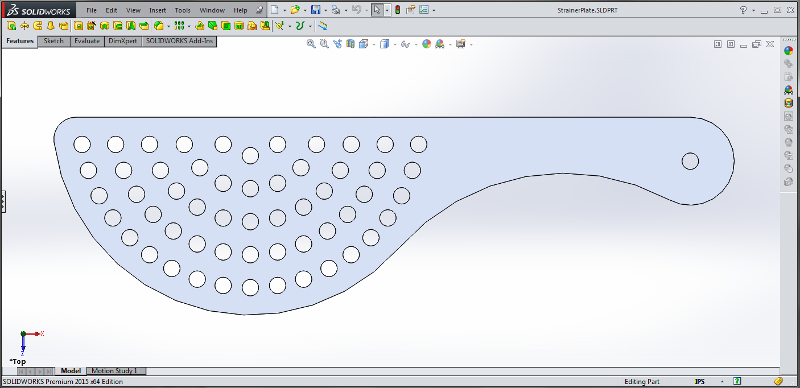
I went through a few iterations of printing it out and holding the paper cutout in my hand to make sure I got the proportions right and eventually converged on an exact model.
I ordered some 3/16" thick aluminum flat bars off ebay and taped a 1:1 scale printout of the design to the top one.
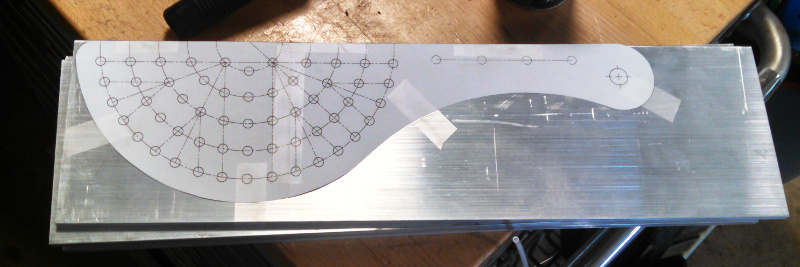
Then I center punched where everyhole would go.
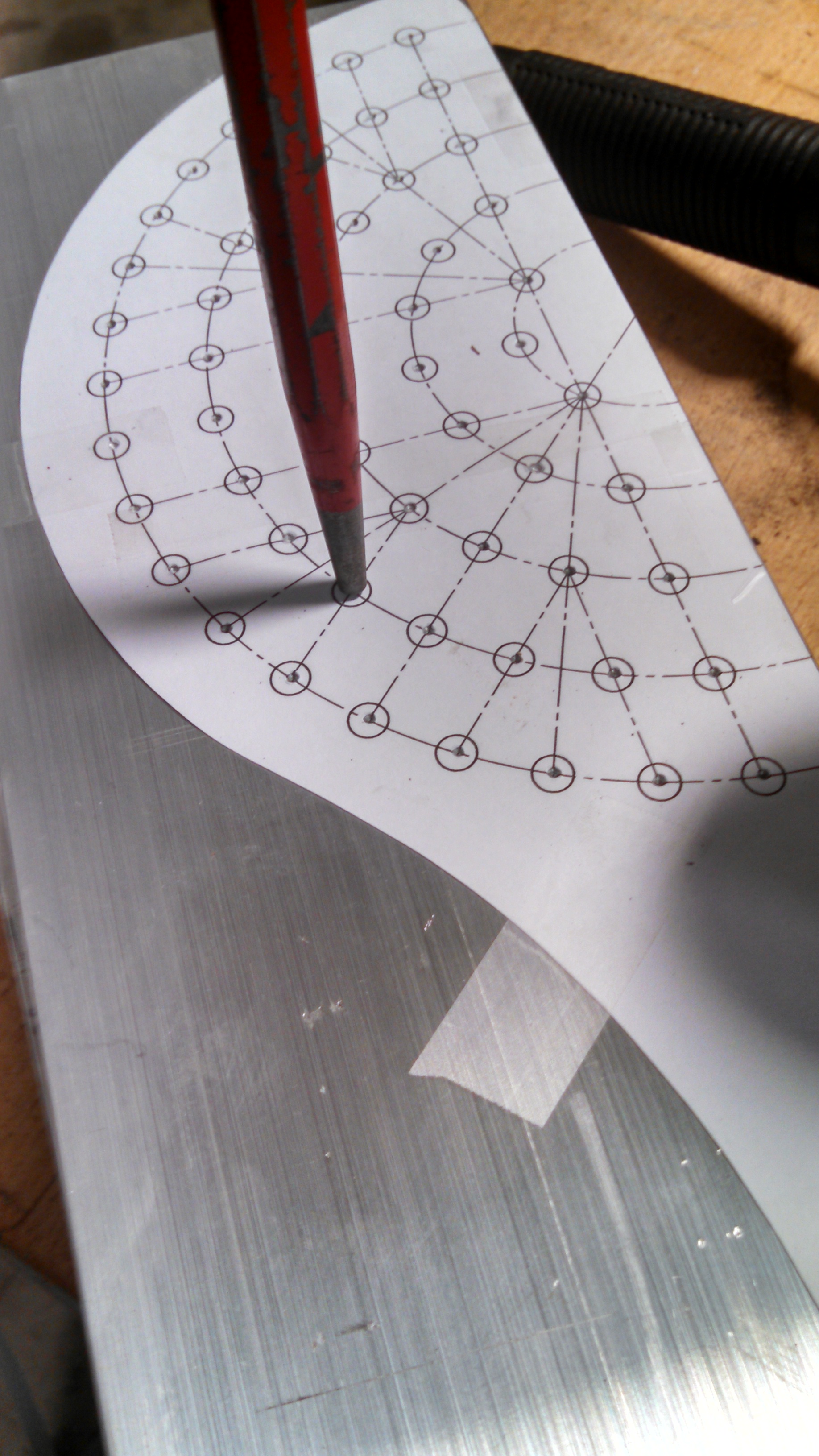
I traced the outline with a marker and then tore the paper off and spot drilled each punch mark. After spotting the pattern I drilled out the whole stack at once with the full size drill.
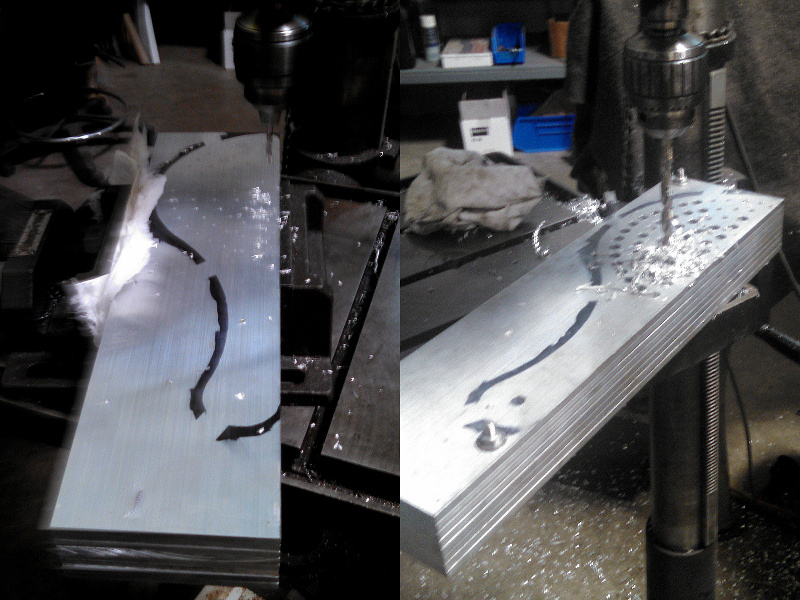
Then because I don't currently have a place to setup my vertical bandsaw I cutout each strainer using my handheld bandsaw. It isn't the best solution but it sure beats doing it by hand.
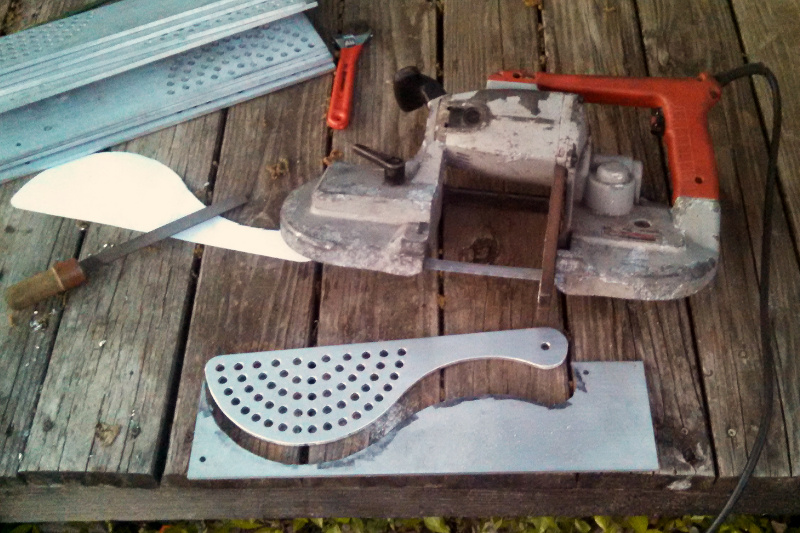
Now I have a whole bunch of cutouts with rough, sharp edges. I wanted to radius or chamfer all these edges so they don't cut anyone so why not make a router bit that does both sides at the same time?
I keep some annealed A2 steel rod on hand for just this purpose so I threw some in the lathe and started turning my tool.
I turned a 1/4" shank to match my router and then used a form tool I already had lying around to create the profile that would radius both side of my parts.
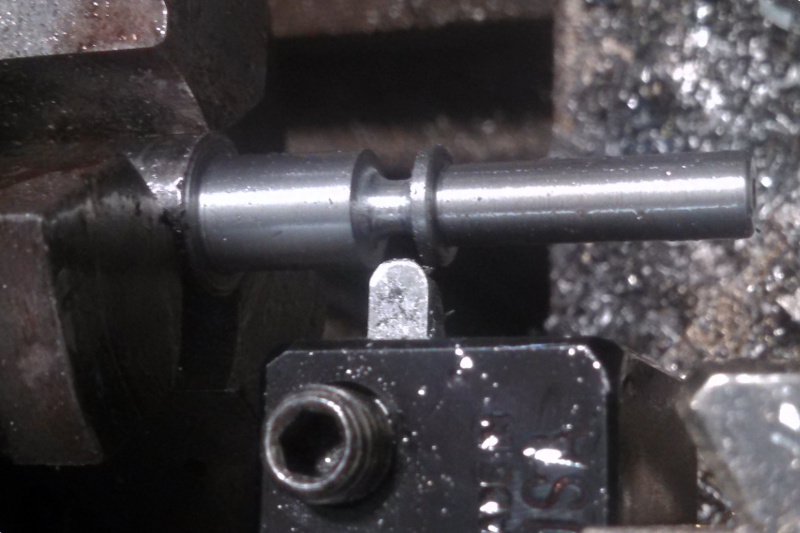
Just part that puppy off.
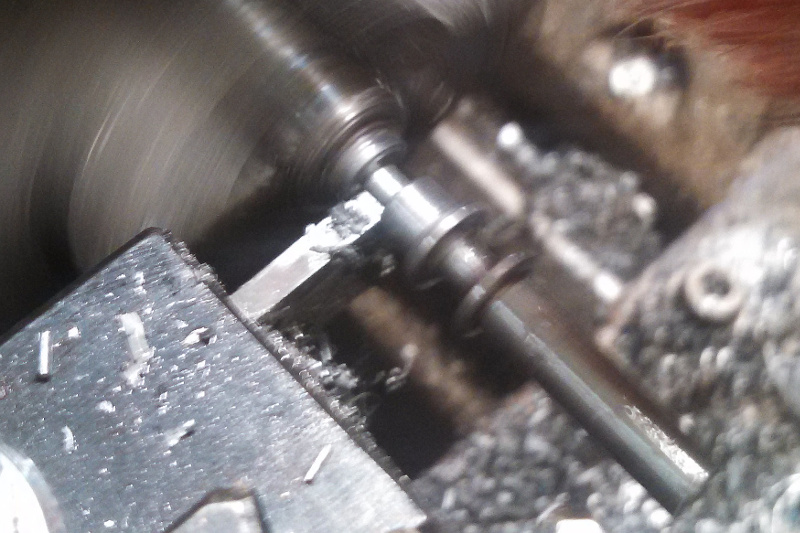
And head over to the mill to gash it and form the teeth.
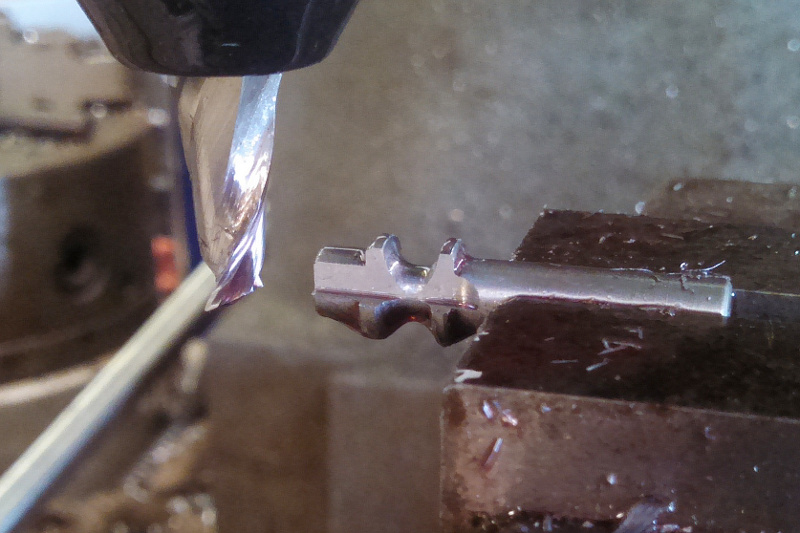
I carefully dialed in the mill to make a cut on centerline that didn't cut into the material at the bottom of the radius at all. I decided on making three teeth but just indexed those around by eyeball since the exact location of each tooth wasn't really important.
After I was done on the mill I heated the tool up to temperature with an oxy-acetelyne torch and let it cool in air. Then I ground relief for the cutting edge by hand on each tooth.
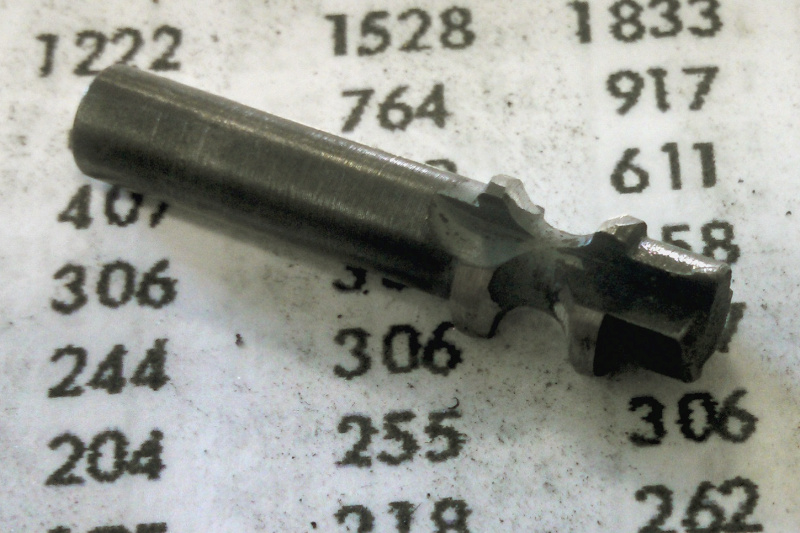
So now I had a finished tool and could get back to the strainers. Not so fast. I had made a stupid mistake when making my tool and the radius was thinner than my aluminum stock!
That made me feel pretty stupid.
I decided not to spend time making another tool, instead I decided to use a router bit I already had to roundover each side separately.
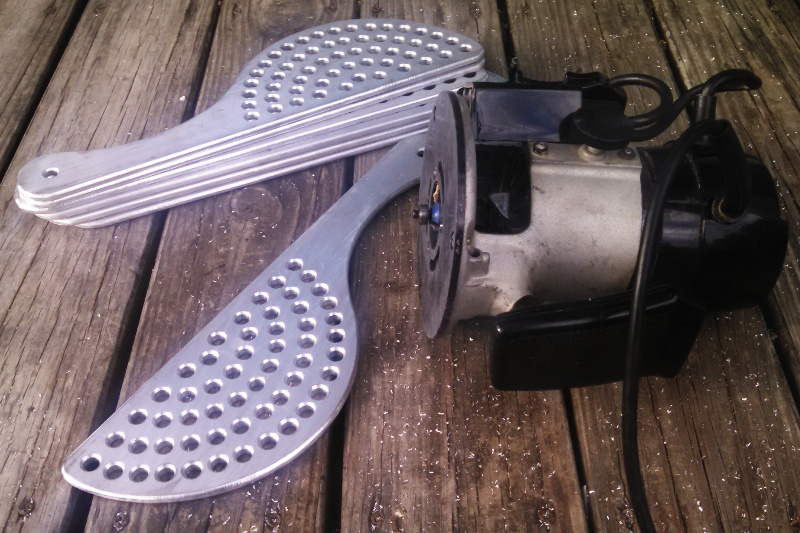
It wasn't perfect but worked good enough. There was one problem though, I couldn't do the hole because the bbearing on the router bit was to large to fit through the holes.
That is easy though, I just threw them on the drill press and chamfered each hole with a countersink. YOu have to be careful to get the depth the same for each hole but it goes quickly.
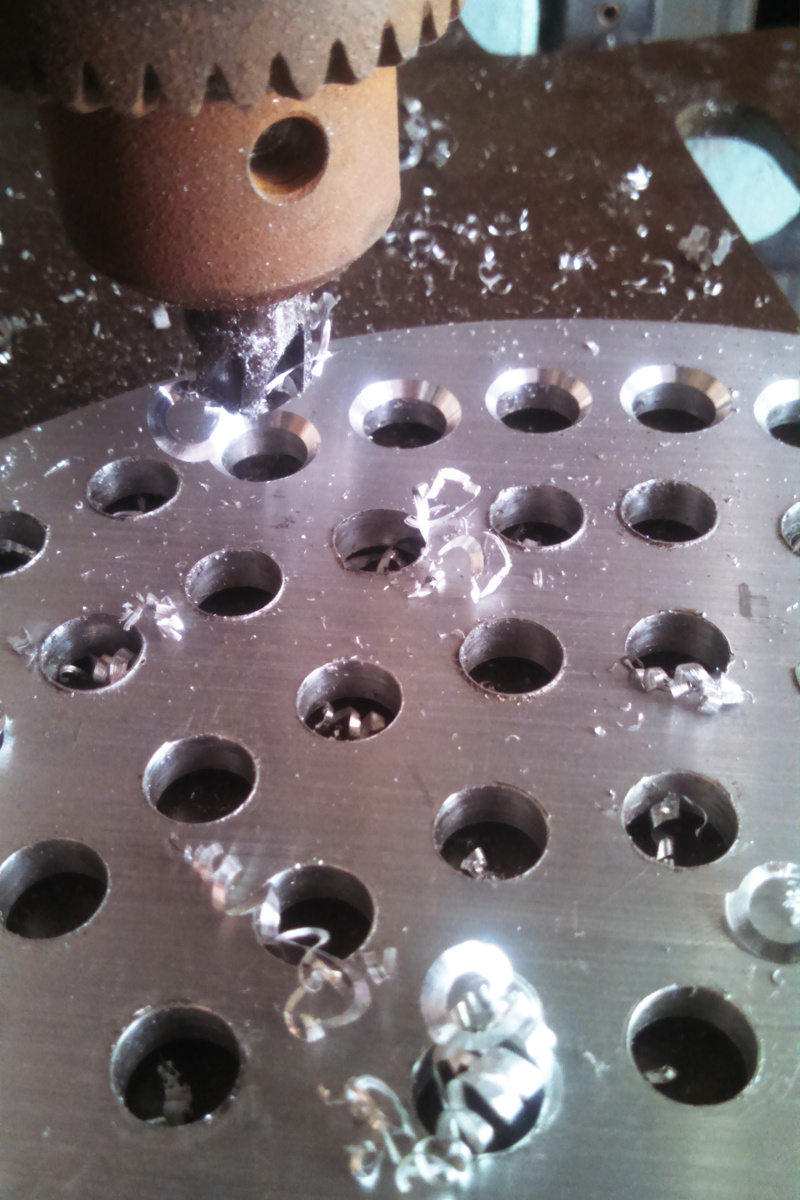
A little handwork with the file and then a quick hit with the belt sander to remove all scratches yields a finished product:
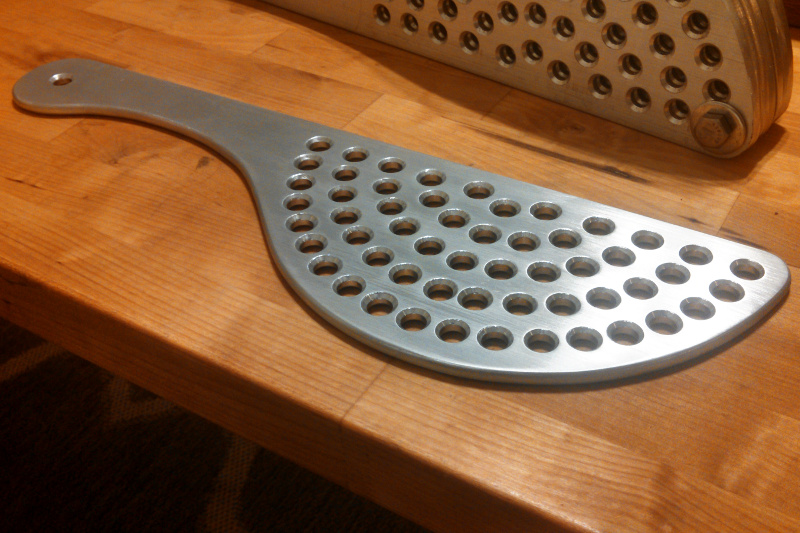
I have been quite happy with the result. They are the right size, feel great in the hand and don't burn you at all(I was a little worried when I started). If I am honest though the holes could be a little bit smaller. They look good and don't spill as much as you might think but some of the smaller pasta shapes squeeze out occasionally.